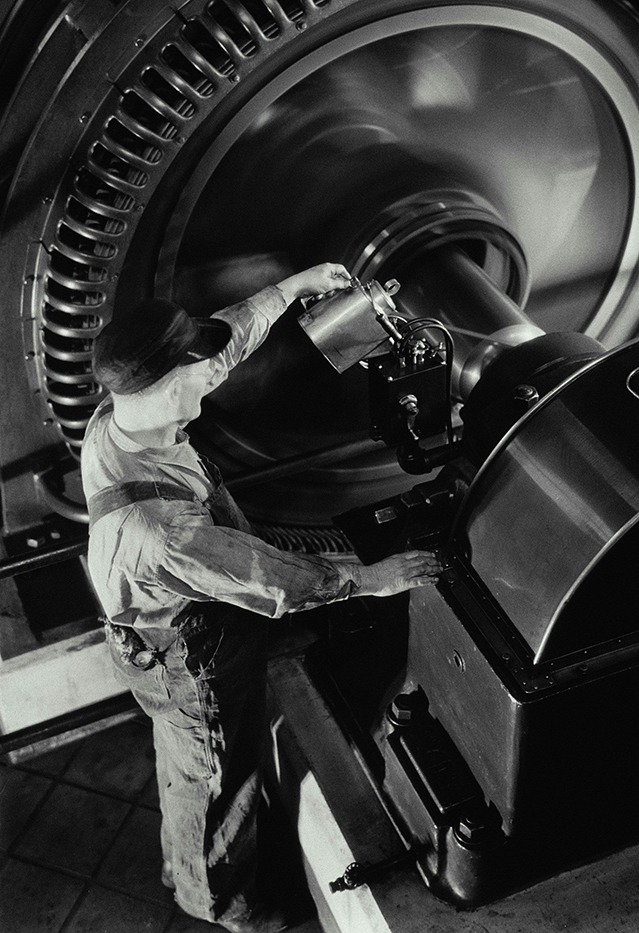
In today’s industrial world, enhancing efficiency and sustainability is more important than ever. Predictive maintenance empowers managers to foresee equipment issues before they lead to costly breakdowns. By analyzing data and identifying patterns, businesses can prevent unplanned downtime, extend the life of their assets, and keep operations running smoothly. This proactive approach not only saves time and money but also optimizes the use of data and resources. In this article, we’ll explore how predictive maintenance transforms asset management and boosts overall operational efficiency.
What is Predictive Maintenance?
Predictive maintenance uses data analysis and predictive modeling to determine equipment maintenance needs. Instead of fixed schedules or reacting to breakdowns, it forecasts potential failures. This proactive approach saves time, money, and resources. It helps avoid unplanned downtime and maximizes asset performance.
How Predictive Maintenance Works
Predictive maintenance uses sensors attached to machinery. These sensors monitor operating conditions and gather real-time data. They track factors such as temperature, vibration, and oil quality. The sensors perform condition monitoring for machinery health.
This data flows into a central system. Software uses machine learning algorithms to detect patterns and anomalies in the collected data from the sensors. When conditions signal a potential issue, a work order is triggered. This system flags issues and enables preventative maintenance, preventing costly breakdowns. Maintenance activities can be better managed with this valuable data, impacting overall maintenance management.
Benefits of Predictive Maintenance
Predictive maintenance offers several financial benefits. These include reduced maintenance costs and increased machine lifespan. A 2022 Deloitte report shows improvements for companies using it. One example highlights a 38% reduction in maintenance costs by monitoring drilling equipment parameters.
Predictive maintenance is most useful for expensive, essential assets. Regularly monitoring asset condition makes a real difference for such assets. This method improves equipment health by decreasing production downtime, while helping improve supply chain efficiency through reduced downtime. These applications result in 33% fewer manufacturing defects, 27% lower maintenance costs, and a 60% longer equipment life.
Downtime losses are significantly reduced due to timely maintenance tasks. Predictive maintenance also optimizes maintenance schedules. This optimizes equipment efficiency and ensures long-term reliability. This includes failure mode analysis to prevent unplanned downtime from various failure modes. The goal is improved asset management leading to better actionable insights.
Predictive Maintenance Techniques
Various predictive maintenance types exist to suit different organizations. Choosing the right technique depends on specific equipment needs. These diverse approaches to predictive maintenance offer tailored solutions to various industrial challenges.
Vibration Analysis
Vibration analysis is critical for rotating machinery. Sensors detect subtle vibration shifts, revealing issues like misalignment or wear. Early detection prevents significant problems, improving overall equipment performance. The failure mode can also be found through analyzing these shifts, which improves equipment health insights and maintenance management systems.
Oil Analysis
Oil analysis checks lubricant samples for wear particles and oil degradation. This simple method assesses the condition of gears, bearings, and other moving parts. It allows for corrective maintenance before major issues arise.
Thermal Imaging
Thermal imaging uses infrared cameras to find hot spots. These areas could indicate friction, overheating, or component failures. Thermal imaging is valuable for identifying minor issues and cost savings on energy use before failures occur.
Acoustic Analysis
Acoustic analysis uses microphones to detect subtle machinery noises. Unusual sounds provide early warnings of potential failures. This proactive approach can avoid unplanned downtime by implementing timely corrective maintenance. Addressing these issues avoids significant production downtime.
Implementing Predictive Maintenance
Implementing predictive maintenance involves a few steps. This structured approach helps integrate new technologies and methodologies efficiently. The end goals are maximizing the returns from predictive maintenance efforts while preventing issues with asset health.
- Install Internet of Things (IoT) Devices: Integrate sensors and IoT technology with your maintenance program. Ensure stakeholder buy-in to maximize program effectiveness. The implementation of IoT devices offers real-time monitoring and actionable insights for optimizing equipment performance.
- Gather Data: Collect historical and real-time data. This data forms the foundation for analysis and model building in the subsequent steps.
- Choose a Platform: Select a platform that handles data sources and performs analysis. It should build machine learning models using real-time data to predict and prevent issues.
- Establish Metrics and Collect Data: Define key performance indicators (KPIs) for your program and collect data from various sources. Ensure data quality for accurate insights into your equipment health.
- Data Preparation and Model Selection: Clean and prepare collected data, select relevant features for prediction, and choose appropriate machine learning tools. Effective data analytics requires integrating various maintenance data sources and choosing the most insightful tools.
- Model Training and Deployment: Train and deploy your chosen predictive models and implement necessary changes to your maintenance processes. Assigning clear roles to your staff enhances the program's operational efficiency.
- Launch and Monitor: Roll out your program and monitor its performance continuously. Adapt your strategy as needed to optimize the program and observe returns on investment. Implement a structured program for managing maintenance activities across the team.
Organizations have used predictive maintenance tools since the early 2000s, according to sources. A 2001 study offers examples of early successes, including analyzing bearing defects through vibration monitoring. Such proactive monitoring of asset condition provides actionable insights for efficient maintenance management.
Challenges of Predictive Maintenance
Predictive maintenance has some challenges. These potential roadblocks include upfront costs and system integration complexity. Addressing them ensures successful program implementation and long-term benefits.
- High initial costs for implementing. Consult with equipment manufacturers and industry experts to understand and manage costs. Strategize which maintenance approaches suit different assets. A basic strategy may suffice for inexpensive parts with readily-available replacements.
- System complexity: Integrating software and sensors with existing technology like Enterprise Resource Planning (ERP) requires specialized training and tools. Encourage a cultural shift in using and interpreting new data. Leadership support for continuous learning is crucial for success, but also costly as these technologies must be regularly audited and revalidated. Visual dashboards showing real-time monitoring data can facilitate discussions about program progress.
The US Department of Energy highlights the benefits of predictive maintenance planning. It notes the potential to eliminate equipment failures and achieve substantial cost savings. These savings range from 8-12% over preventive maintenance to 30-40% compared to reactive maintenance (source). Utilizing condition monitoring data allows businesses to further enhance these cost savings and minimize unplanned downtime by incorporating maintenance work based on asset condition, ultimately streamlining production hours.
The Future of Predictive Maintenance
Predictive maintenance is rapidly growing. Market Research Future projects the global market to surpass $23 billion by 2025. Companies can gain a competitive edge by embracing this technology. It’s essential for staying competitive as technology costs decrease.
McKinsey Global Institute predicts connecting assets through the Internet of Things will significantly boost the global economy. This impact is estimated at $11 trillion annually by 2025. The integration of iot sensor data helps achieve better predictive data accuracy for maintenance predictions and prevents costly downtime.
Deloitte’s chart shows how each industrial revolution improved equipment effectiveness. Linking global assets with machine learning improves asset health predictions. BMW's connected welding guns demonstrate this, collecting vast datasets for accurate condition and future state assessments. Artificial intelligence plays a critical role in enhancing insights about real time equipment health and improving long-term maintenance planning.
Predictive Maintenance for Operational Excellence
Predictive maintenance transforms business operations. From factories to fleets, it saves money, extends equipment life, and increases efficiency. As adoption increases, embracing predictive maintenance offers significant future benefits. Implementing it improves asset performance, streamlines scheduled maintenance, and offers valuable insights from oil analysis and other predictive data sources. Now, more than ever, embracing a proactive approach that employs vibration analysis in a well-structured predictive maintenance program can enhance your equipment health monitoring. Don't wait - begin incorporating these valuable strategies to refine your maintenance predictive approach and optimize spare parts management. By integrating predictive maintenance effectively within your existing asset management systems, you can effectively allocate maintenance team resources, enhance real-time monitoring, and make data-driven decisions.
Ready to get started with predictive maintenance? At Ameta, we specialize in cost-effective, tailor-made solutions that increase efficiency and reduce costs. Contact us today to discover how we can help you optimize asset performance and secure a competitive edge in your industry!