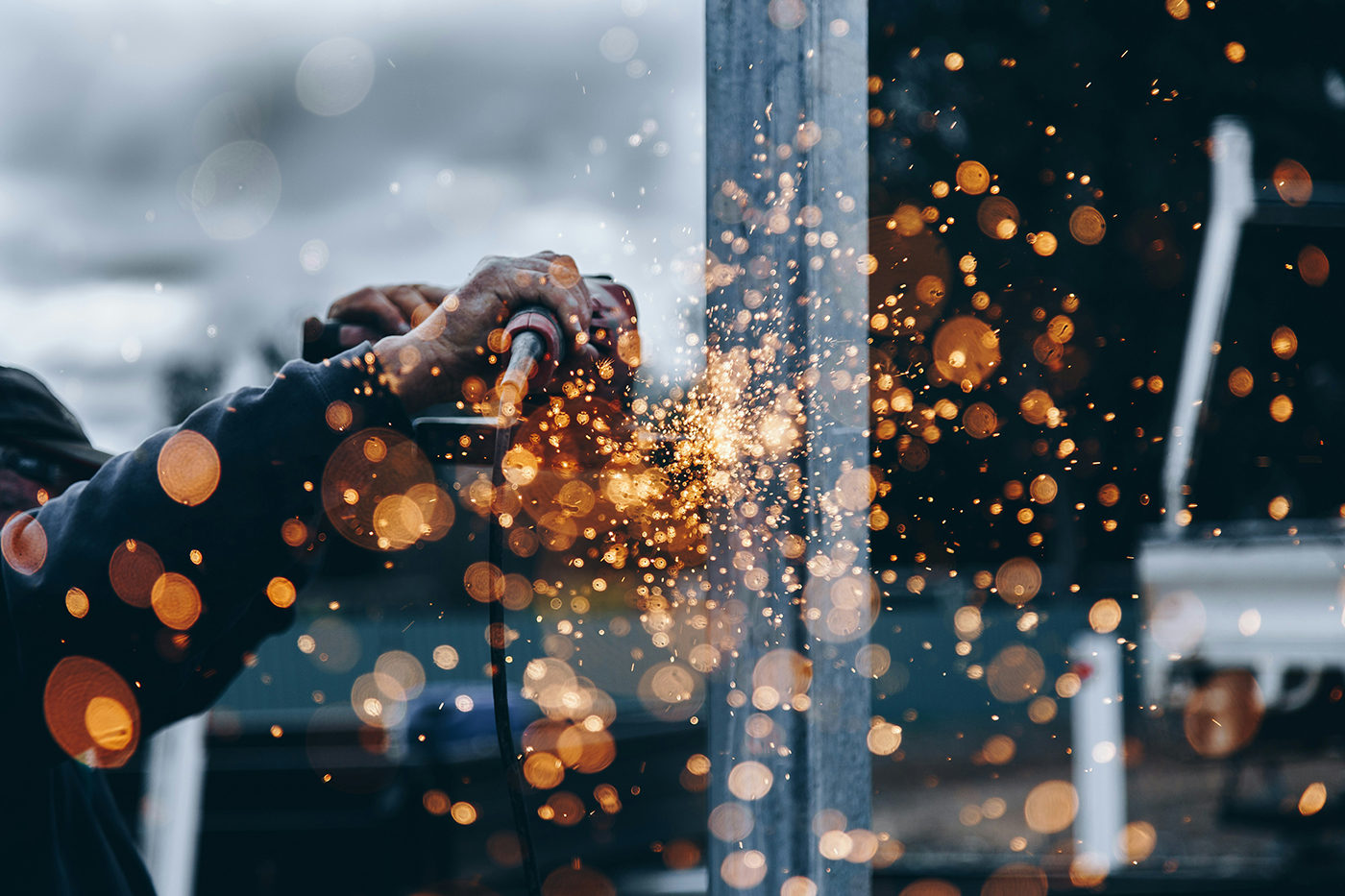
In today’s competitive landscape, optimizing operational efficiency is paramount. Predictive maintenance cost savings offer a powerful approach to streamlining processes, minimizing downtime, and boosting your bottom line. This proactive maintenance program uses data and insights to transform your maintenance strategy, shifting from reactive break-fix scenarios to proactive, planned interventions. This fundamentally alters how you approach asset management and cost reduction.
Understanding Predictive Maintenance
Predictive maintenance uses data analysis, machine learning, and sensor technology to anticipate equipment failures before they happen. This allows for timely interventions, optimizing maintenance schedules, and maximizing equipment life. This differs from traditional reactive or preventive maintenance approaches.
How Predictive Maintenance Works
Predictive maintenance relies on data from sensors embedded within equipment. These sensors gather real-time data on various parameters like temperature, vibration analysis, and oil quality. This data feeds into analytical models.
Combined with historical data and performance trends, these models identify patterns and anomalies that may indicate impending failures and potential failures. This helps reduce downtime costs by addressing issues proactively.
Through sophisticated analysis, predictive maintenance pinpoints potential failure points. This allows maintenance teams to schedule repairs precisely when needed, aligning with production needs and available resources. The ability to predict equipment failures and predict equipment issues through a maintenance program dramatically changes the maintenance strategies your team employs.
Predictive Maintenance Cost Savings: Unveiling the Financial Benefits
Predictive maintenance can reduce maintenance expenditures. Compared to traditional preventive maintenance practices, it can lead to savings between 18% and 25%. Research from McKinsey highlighted a potential reduction in unplanned downtime with more focused interventions. These maintenance practices are truly data-driven decisions to generate substantial savings. By utilizing maintenance sensors to better understand equipment vibration, we can further maximize equipment life, effectively implement cost-effective maintenance, and truly transform your facility’s maintenance management.
Minimizing Downtime and its Associated Costs
Unplanned downtime drains resources. It causes lost production, missed deadlines, and reduced profits. The True Cost of Downtime report shows substantial manufacturers lose many productive hours annually. Each hour translates into significant revenue loss.
Predictive maintenance addresses this by identifying and mitigating failures. It minimizes downtime cost and unnecessary equipment repairs. Plus, it improves asset performance for substantial savings. Proactive maintenance prevents small issues from becoming large problems. By taking proactive measures and identifying early signs of deterioration, predictive maintenance extends the life of your equipment.
With early detection of potential failures, businesses can extend the lifespan of their equipment, and significantly lower repair costs and reduce maintenance costs associated with premature failures. Addressing maintenance activities proactively ensures equipment is functioning reliably and consistently throughout its lifecycle, reducing the impact of maintenance costs on overall operational budgets.
Optimizing Maintenance Spending and Resource Allocation
Traditional preventive maintenance can lead to unnecessary expenditures. Sometimes maintenance is performed too frequently or without justification, wasting around 30% of preventive maintenance funds. A predictive maintenance plan offers more cost-effective maintenance with a data-driven approach. Predictive maintenance cost savings mean fewer expenses and better decision-making in maintenance activities. Using vibration analysis and historical data you can reduce maintenance costs.
Predictive maintenance allocates resources strategically, focusing maintenance work only on equipment needing attention. This reduces waste and improves cost-effectiveness. Accurate procurement of spare parts becomes possible with real-time insights. Using data analytics to determine the best time to service equipment maximizes uptime and creates savings. This leads to a decrease in downtime cost and overall enhanced asset performance.
McKinsey’s 2018 study on predictive maintenance explains its various benefits. Predictive maintenance implementations can reduce carrying costs up to 20% where sensors aren’t necessary. It offers an effective maintenance plan compared to traditional methods and even other preventative maintenance approaches.
Extending Asset Lifespan and Reducing Replacement Costs
Timely maintenance prevents breakdowns and extends asset life. Predictive maintenance uses the Internet of Things (IoT) for early detection of wear and tear. This allows proactive measures to prolong the lifespan of equipment and enhance product reliability.
Predictive maintenance pinpoints issues in real time, proactively indicating how long equipment will operate before breaking down. This facilitates optimal inventory management, ordering replacement parts only when needed, generating substantial cost savings. These savings predictive maintenance programs offer will be substantial for any facility management.
Extending the operational life of assets postpones replacements and reduces downtime. It enhances sustainability by minimizing manufacturing and operational risks throughout the product lifecycle. A well-defined maintenance plan plays a critical role in identifying potential risks and avoiding unexpected equipment failures. Through predictive maintenance, not only can you anticipate and mitigate potential problems, but you can also improve asset performance over its lifetime, thereby enhancing overall product reliability and minimizing the risks associated with unexpected equipment downtime.
Implementing Predictive Maintenance: A Practical Roadmap
Implementing predictive maintenance requires planning. Consider these factors for cost-effective maintenance solutions.
- Identify Critical Assets
Focus on assets with the highest operational impact and downtime risks to ensure resources are allocated effectively. - Select Compatible Sensors
Choose sensors that seamlessly integrate with existing systems for accurate, real-time data collection. - Develop Analytical Models
Use historical and real-time data to build models that effectively interpret performance patterns and predict failures. - Invest in Workforce Training
Equip your team with the skills needed to execute predictive maintenance strategies effectively.
Real-World Examples of Predictive Maintenance Cost Savings
Businesses across sectors successfully employ predictive maintenance.
- A manufacturing company reduced downtime on assembly line robots by 15% using predictive maintenance, saving millions annually.
- A transportation company lowered fleet maintenance costs by 20% and improved fuel efficiency with predictive maintenance algorithms.
Driving Operational Success with Predictive Maintenance
Predictive maintenance cost savings offer more than financial benefits. They reshape asset management and maintenance procedures, leading to efficient inventory control and improved resource allocation. By minimizing downtime and reducing maintenance spending, predictive maintenance offers substantial savings. The resulting increased savings allows for better cost management. By using data to make informed decisions, you can streamline your operations. Predictive maintenance helps identify potential issues early on.
Predictive maintenance positions your company for peak production, high efficiency, and maximum output while reducing production risks. It generates substantial savings while improving asset performance and achieving effective maintenance. Embracing predictive maintenance can lead to improved inventory control, reduced waste of resources, increased operational efficiencies, substantial financial benefits, and long-term sustainability. The time predictive maintenance saves is also a huge asset.
Take the Next Step with Ameta
Curious about how predictive maintenance can transform your operations? Discover innovative solutions tailored to your needs with Ameta. Contact us today to learn more and take your efficiency to the next level!